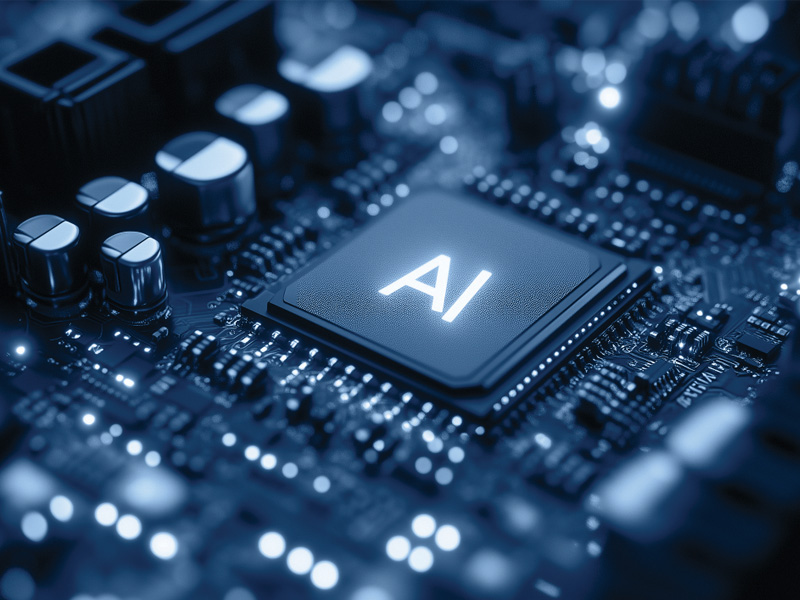
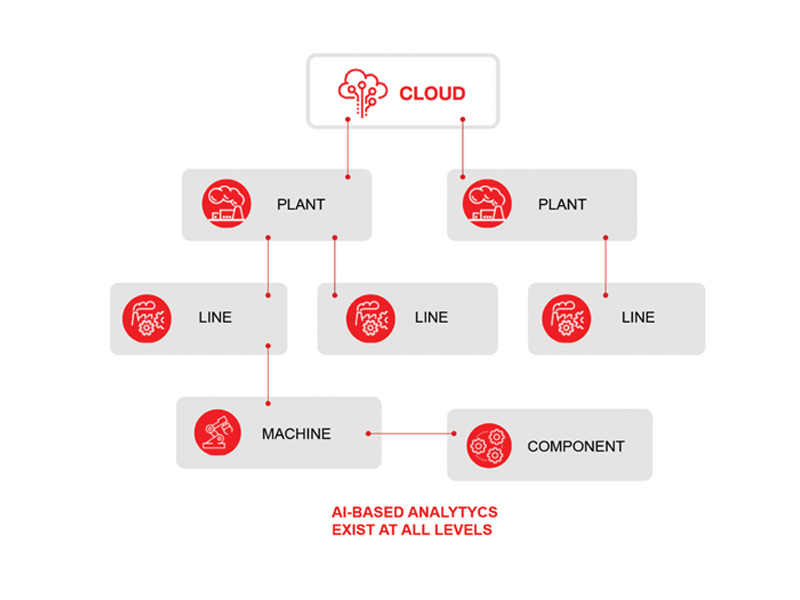
Common issues such as high initial costs, complex implementation processes, and long turnaround times continue to be major obstacles to AI applications in the manufacturing sector. Mitsubishi Electric emphasizes that AI applications are not limited to cloud-based systems.
The company is making it possible for manufacturers of all sizes to benefit from AI at a low cost and effectively with a strategy that starts at the component level and progresses incrementally.
Intelligence Has Dropped to the Component Level
A significant portion of the failures that occur in production facilities can be predicted by analyzing data collected from components. At this point, advanced analysis performed in servo drives allows automatic diagnosis of potential problems in surrounding machine parts. While frequency inverters use artificial intelligence algorithms to detect the root causes of failures, industrial robots increase both productivity and improve quality thanks to real-time route optimizations.
One of the most important advantages of this approach is the ability to respond immediately to abnormalities in equipment or to predict them in advance. Smart components equipped with artificial intelligence can analyze data in real time and quickly adjust parameters if necessary or disable the system to prevent a major failure.
Mitsubishi Electric Factory Automation EMEA Digital Marketing Director Piotr Siwek, who made an assessment on the subject, said, “The common point we have observed in production facilities of different sizes is that AI-supported components significantly reduce unplanned downtime. This system provides an advantage by working completely automatically. Analysis is performed automatically in the background without the need for data science knowledge.”
From Smart Components to Digital Factories
1,350 teammates, our production facilities with modern technologies and green energy. “We will continue to work and invest to maximize the contribution we provide to our country and industry in the coming period,” he said.
The scalable structure offered by this approach, which starts at the component level and spreads to the production line, makes it possible to act at much lower costs compared to public cloud solutions when implementing artificial intelligence applications. Intelligence applications that start at the component level, combined with PLC control systems integrated into the production line, pave the way for holistic data analysis. In today’s world where data needs are increasing, it is possible to process all data within the factory with edge solutions. This local processing approach also provides a significant advantage in terms of data security. In production facilities that work with sensitive technology and data in particular, not exposing data to the outside also reduces the risk of cyber attacks and data breaches.
Siwek summarizes an example of the field applications of this strategy as follows: “We started artificial intelligence analyses in welding applications in a factory in Europe. The edge-level analyses performed with MaiLab provided almost 100% accurate failure prediction. Thanks to these successful results, the customer decided to spread the project to the entire production line. The path to success is to start with small and measurable projects.”

Hybrid AI Models Are Increasingly Important
Industry experts predict that hybrid AI solutions will become more prominent in the future. These approaches combine component-level analysis with selective cloud use, providing manufacturers with flexibility and in-depth analysis. When it comes to issues such as historical data analysis covering multiple facilities or supply chain optimization, cloud solutions offer an ideal infrastructure.
Cloud technology provides unique capabilities in advanced applications such as big data analytics and machine learning.
Especially for global companies that manufacture in multiple locations, comparing and improving processes simultaneously can be carried out much more effectively via the cloud.
Siwek points out that customers who have established strong digital foundations starting from the component level can consciously choose which processes need cloud support.
The Future of Digital Transformation: Scalable Artificial Intelligence
This evolutionary AI approach, which starts at the component level, offers a sustainable solution not only technologically but also strategically. This model, which allows for the step-by-step development of digital capabilities without high investment risks, also provides rapid returns. Over time, as the organization and analysis needs grow, the system can be expanded with new layers; selective cloud solutions can also be integrated into this expansion process.