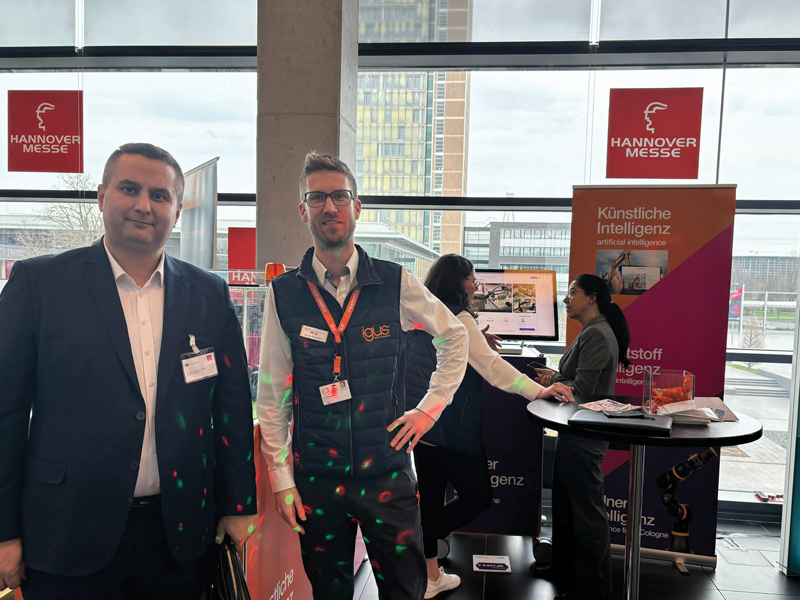
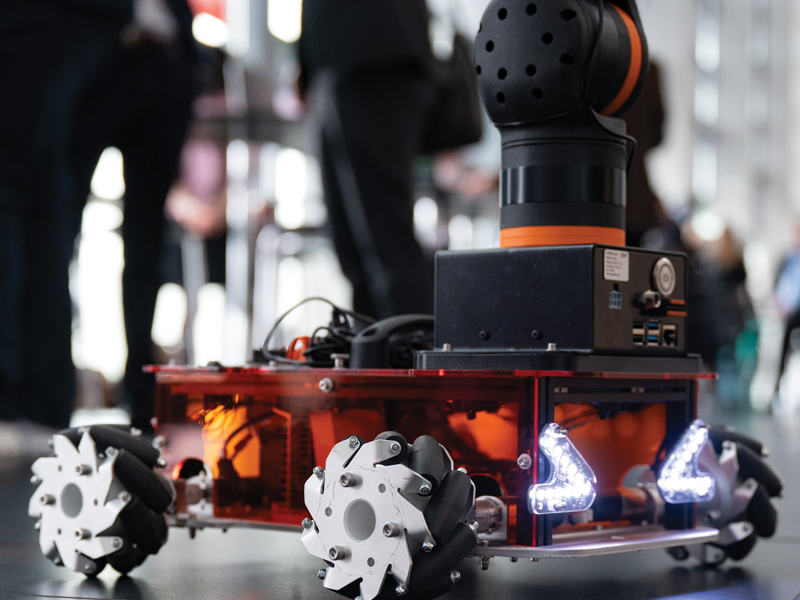
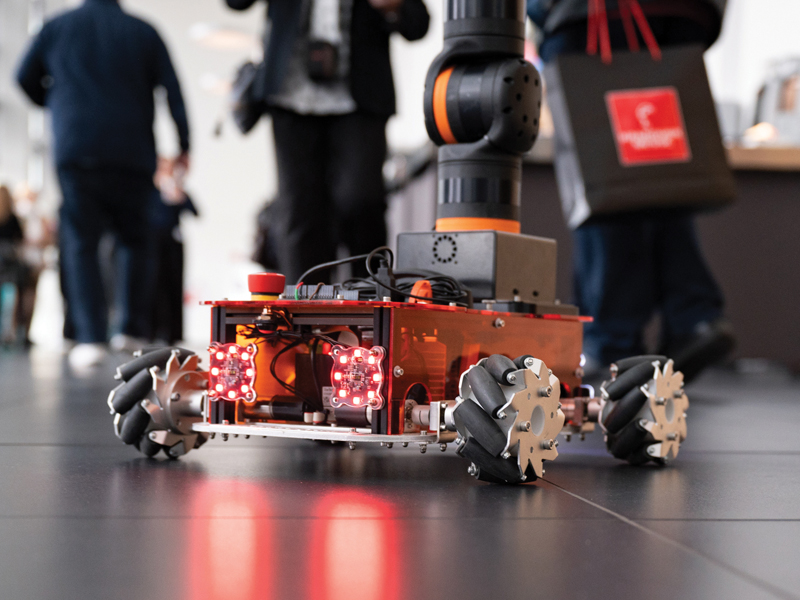
Smart maintenance, low-cost robotics, AI-based online tools: igus is showcasing pioneering solutions for the lubrication-free and CO2-neutral industry and automation of tomorrow at the Hannover Messe
Cologne/Hanover, 21st February 2024 – To support industrial companies with the challenges of our time, such as the transformation to Industry 4.0 and CO2-neutral production, Cologne-based motion plastics specialist igus is relying on triple intelligence at the Hannover Messe: artificial intelligence, plastics intelligence and Cologne intelligence. The exhibits include smart sensor technology for the maintenance of tomorrow and AI-supported low-cost robotics that are easy to operate. igus will also be presenting an AI-based app that shows design engineers the optimisation potential of their application with lubrication-free motion plastics in a matter of seconds.
Artificial intelligence (AI), machine learning, digital twins: innovative technologies are revolutionising the way industrial companies manufacture their products and optimise processes. Artificial intelligence simplifies the work of designers right from the selection of suitable components. igus proves this at the Hannover Messe with igusGO. It only takes the AI-based app seconds to reveal how an application can be technically optimised with lubrication-free components from igus. To do this, designers don’t have to pore over catalogues, make phone calls or write e-mails, but simply take a photo of their application. The app uses AI algorithms to recognise the object and makes suggestions for igus products that increase reliability and reduce costs. In the case of a bucket wheel excavator, for example, these could be heavy-duty bearings made of high-performance plastic. For the first time, a new study carried out by scientists at RWTH Aachen University and igus has now quantified the economic and ecological benefits of lubrication-free polymer bearings: depending on the application, this saves between €7,000 and €14 million per year otherwise spent on lubricants. At the same time, dispensing with lubricants offers potential CO2 savings. Study participant Heineken Brasil, for example, saves 180kg of CO2 equivalents per year by using polymer bearings. “If all Heineken branches were to switch to polymer bearings, the company could save 28,814kg of CO2 equivalents. A small modification with great effect. “The potential for optimisation by using our motion plastics can be discovered much more easily and quickly with the help of igusGO. We launch numerous innovations every year - in 2023 alone, there were 227.
Our AI app now makes it possible to navigate through our ever-growing product cosmos with maximum efficiency and transparency,” says Tobias Vogel, CEO Plain Bearings and Linear Technology at igus. There are already over 580 different applications in the app’s brain, and the number is growing every day – from coffee machines and crane systems to aeroplanes.

Plastics intelligence for an easy and cost-effective entry into predictive maintenance
Plastics from igus are also intelligent. At Hannover Messe 2024, igus will present smart plastics, i.e. energy chain systems, cables, linear guides and plain, spherical and slewing ring bearings equipped with intelligent sensors. They not only enable real-time condition monitoring but can also be connected to various networks and IoT systems. This means they can be integrated into a predictive-maintenance concept to avoid expensive production downtimes caused by unplanned plant shutdowns. Sensors, evaluation modules and software enable a dynamic service life calculation and help define optimum maintenance times for the products - which also offers an advantage in terms of sustainability. The reason is that products are not replaced unnecessarily or too soon, but only when they have reached the end of their product life cycle.
However, that’s not all: igus is continuously developing their smart plastics services in response to current challenges such as the shortage of skilled labour. Thanks to the digital service called superwise, for example, it is now possible to keep a constant eye on your own applications via a central dashboard with less personnel than ever before. The intelligent linking of application, product and sensor data in addition to the optional use of the Internet of Things results in comprehensive “plastics intelligence”. The customer automatically receives timely maintenance recommendations, offers, warnings or suggestions for improvement. If companies don’t have time to keep an eye on their applications themselves, igus takes on this responsibility. Employees reach out proactively when something needs to be done. Says Michael Blass, CEO of E-Chain Systems at igus: “The superwise service combines the modern sensor technology of smart plastics with an all-round digital service. In times of multiple crises, it is digital innovations like these that are more decisive than ever for the competitiveness of companies. It is important to us that small and medium-sized companies without in-depth expertise and with low budgets can also benefit from trends such as predictive maintenance.”

Operating low-cost robots easily with AI-based voice and gesture control igus will also be presenting new products in the field of low-cost automation at Hannover Messe 2024. This is where Cologne intelligence comes into play. All robots at igus are “made in Cologne” – from injection moulding and assembling circuit boards to programming. This includes the ReBeL cobot, which is available in the fully equipped plug-and-play version for just €4,970. For users looking for an even more compact solution, igus has developed the ReBeL KID.
Visitors to the preview will already be able to see an Education AGV, an open-source solution and autonomous learning platform consisting of an automated guided vehicle system (AGV) that can be combined with cobots such as the ReBeL or ReBeL KID. Customers can combine compatible low-cost accessories from over 100 manufacturers, such as grippers or vision systems, via the RBTX online marketplace via plug and play - supported by online tools and 3D models. RBTX is designed to enable companies of all sizes to get started with automation at low cost. Artificial intelligence also plays an increasingly important role here. AI can help develop an automation solution more quickly and easily, for example with AI-based simulations. Customers don’t have to purchase a robot and put effort into its integration, but can test their application in advance.
In addition, igus offers products with AI-based voice and gesture control. You can connect Amazon Alexa directly to the igus robots or integrate gesture control via ROS 2. This will make it really simple to define the movements of robots in future. Such AI-supported, intuitive operability combined with a low price paves the way for low-cost robotics to enter the mass market. igus currently uses AI primarily to monitor robots and integrate vision sensors quickly and easily. The robotics team, however, is also researching resilient programming using speech or gestures. Simple robot programming for everyone, which is not limited to the robot, but realises the entire application. “Interested parties are always surprised at what igus high-performance plastics can do - whether in terms of freedom from lubrication, CO2 reduction or automation,” emphasises Tobias Vogel. “By combining our innovative products with digital services and new technologies, we want to show that our lubrication-free motion plastics can improve a wide range of applications, making them more sustainable and capable of Industry 4.0,” concludes Michael Blass.