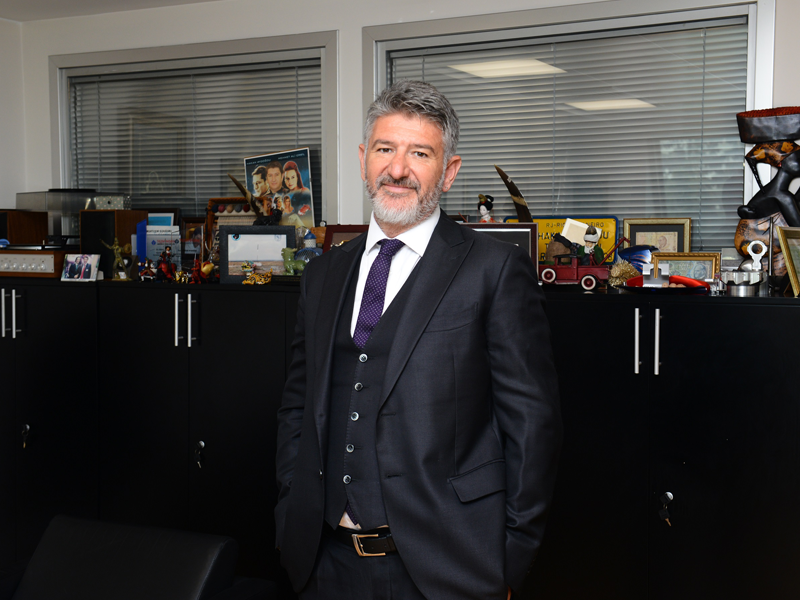
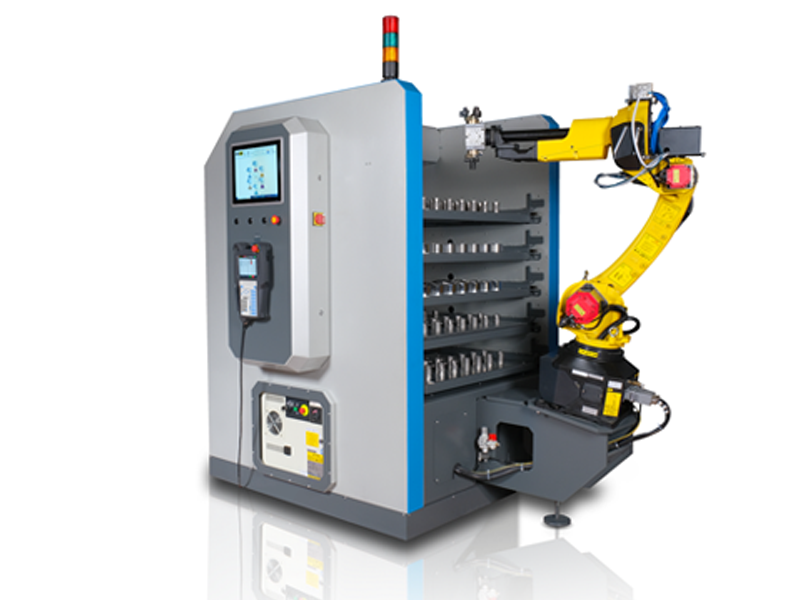
Tezmaksan, the solution partner of the machining industry in Turkey for more than 40 years, helps to carry out tasks such as loading and unloading of workpieces, tool changes, quality checks without any problems, without any problems, thanks to its CubeBOX automation systems for CNC feeding. CubeBOX, which has the “Domestic Production” certificate and is currently exported to 36 countries, also contributes to the sustainability of production by providing industrialists with time and cost advantages at every stage of manufacturing.
Tezmaksan, which continues its technology investments for the competition and high exports of the Turkish machining industry abroad, is investing in the future in higher efficiency production with its robotic automation system CubeBOX. In this regard, Tezmaksan General Manager Hakan Aydoğdu, who evaluated the process of integrating automation into CNC machines, said, “The 2020 In(Sight) report shows that automation is on the rise. While 54 percent of employees believe they can save up to 240 hours a year thanks to automation, 61 percent of business leaders believe automation can be easily implemented in their industry within the next 12 months. CNC machining is no exception. CNC machines come with different levels of software and automation. The specified level of automation can greatly improve machining processes and therefore the quality of manufacturer components. “But the challenge lies in determining the appropriate CNC machine tool and automation for your installation,” he said.
Using CubeBOX is simple even if you do not have robot programming experience
“If you are working with older CNC machine models, automatic tool changes are often not an option. However, if you aim to optimize the cycle time, there are steps you can take to shorten tool change times,” said Aydoğdu, regarding the advantages of the CubeBOX robotic automation system they developed: “Manual replacement of robot components in a system is a job that requires expertise in robot programming.
It leads to both long-term business disruptions and dependence on skilled personnel. Our CubeBOX automation system offers a user-friendly interface that allows operators to effortlessly change parts without any prior robot programming knowledge. This rapid loading and unloading of workpieces significantly increases flexibility and agility in the production process, making it easier to quickly adapt to evolving production needs. Thanks to this automation technology, we enable companies to achieve higher levels of efficiency, precision and productivity in their operations. As another advantage, we help significantly reduce the human intervention required for the machining process. Additionally, thanks to our RoboCAM software program, we enable the installation of a new part in just four steps. “The program is simple and fast to use and can install the part in less than 2-3 minutes.”

CubeBOX makes a difference in production capacity with its 24-hour uninterrupted operation feature
Emphasizing that the manufacturer can reduce labor costs by increasing production capacity by operating CNC machines uninterruptedly for 24 hours, thanks to CubeBOX, Aydoğdu said, “This automation also increases advanced precision and consistency in machining operations. We equipped the CubeBOX with advanced sensors and programming capabilities that allow it to be executed with a level of accuracy that is difficult to do manually. In this way, the system can adapt to various CNC machine types and sizes without any limits, making them suitable for a wide range of applications in different industries. Whether in metalworking, woodworking or other manufacturing sectors, automation can be tailored to meet specific production needs and requirements. In addition, the security problem is eliminated thanks to CubeBOX. With the automation of CNC machines, operators’ difficulties in performing repetitive errors or physically demanding tasks are greatly reduced, thus minimizing the risk of possible accidents and injuries. “This not only protects employee well-being, but also reduces potential downtime and associated costs.”